For those who don't know, I am working towards a AAS degree in Machine Technology. I seem to have a knack for CNC programming, especially hand-code.
SkillsUSA is an organization dedicated to getting people into technical fields, basicly so that there will be a future generation of people able to actually -build- things, and not simply draw stuff up and send it off to China.
How does this affect me? When one teacher at my school who has been involved with this whole program for a while asked for people who wanted to compete in the Skills USA competitions, I volunteered. To make a long story short, I got entered in under "CNC Milling"(which is my strong suite). My machining teacher, Mike, learned that -no other school- in the state was going to compete this year(in this competition), so it was up to Mike to create a competition. He got ahold of the contest rules, and, a day before the contest was supposed to happen, found a print for contestants to make and set things up.
Note that there were three of us, all from my class, competing in this mini-contest. It was practically not even funny - Worst you could do is get to put "3rd place SkillsUSA state CNC milling competition 2009" on your resume.
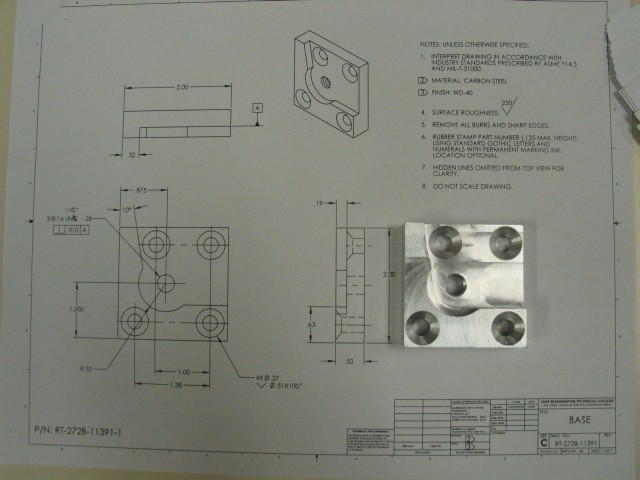
Thursday, all three of us were handed the the print, some instructions, a written test, and then told which CNC machine each of us would be using.
The instructions were as follows:
1. You have 45 minutes to complete the written test, and
four hours to complete the part specified in the print.
2. You must
hand-code your program - No CAD/CAM software.
3. You may setup your machine first, and it will not count towards the four hour limit.
...And then some other stuff of less importance.
We were then told to take a look at the print, find all tools we would need and get our machines ready.
I was told to use our Haas TM-1, which is both the newest, and lightest duty CNC machine we have.

After spending about 2.5 hours getting our machines ready, finding holders for all the tools, getting them in the machine we were done with that.
At this point it was 9:30 AM(Note: we take a break from 9:30-9:50 AM). After break, we came back and took the written test.
I finished my written test in 15 minutes. I then started timing myself for the four hours, pulled up
Discriminator, all my old programs, and got to work.
I had my program completed in one hour.The program does the following:
Tool 1 - 2" carbide facemill:
1. Faces off the top of the block of Aluminum I got(Note: raw dimensions 2.4X2.4X0.9 - part is 2X2X.5)
Tool 2 - 3/4" 2-flute flat endmill:
2. Profiles around the part in two passes(roughing, with a .01 finish pass), using cutter compensation.
3. Comes in from the Y+ direction into the 10deg angle, feeds "down" in the Y-/X+ direction to where it meets the line going straight in the X+ direction, then feeds out of the part.
4. Turns off cutter compensation, clears out the remaining material in the upper right hand corner.
5. Rapids up to .1 above the part, goes over to the center of the circle, rapids out to the left side of the circle(in this case, .125 away from the center - 1"-3/4" = 1/4" / 2 = 1/8" radius), then feeds down, circles 360 degrees in a CCW direction. It then rapids away from the wall/up and out of the hole.
Tool 3 - #3 centerdrill:
1. Centerdrill all 5 holes to .100 into the material.
Tool 4 - drill for 3/8"-16 tap(I forget the size):
1. Drill out tapped hole.
Tool 5 - 3/8-16 tap:
1. Rigid-tap the hole
Tool 6 - .27 drill:
1. drill all 4 other holes
Tool 7 - 5/8 90deg countersink(note - 90deg because we didn't have any 100deg, this was specified in the instructions):
1. Counterbore all 4 holes.
------------------------------------------------------------------
I then wrote a program to face off the other side of the part - basically a copy of the tool #1 code.
Just after I was done, it was Cleanup time(11:30).
On Friday, I came in, started up the Haas, loaded my program, did a couple of minor changes on the machine after running the Graphics test-mode, and ran 3" above the part(to make sure it would do what it should - which it did).
I then told Mike, and got permission to run. Aside from a couple minor issues, like the fact that milling the 10deg angle it was chattering like mad(no matter how I adjusted the speeds/feeds), it ran fine. I stopped the program before the upper two counterbores, as I was worried about it hitting the angle. Mike said to go ahead, and as I had talked to him I wouldn't lose any points if it did. Needless to say, it did.
I was done with my part by 9:30. Less than 3:30 into it, I had actually completed the entire part.
What about the other contestants, you ask?
Contestant #1 got about 3/4ths of the top milled, but all the counterbores came out too deep. Also the angle wasn't right, and the circle wasn't.
Contestant #2 got the best machine, but he ran into issues of not remembering how to code this stuff having gotten lazy and soft using CAD/CAM software for everything. He ended up getting the top, sides, and angle milled.
Needless to say, I took first place. Which means that not only did I end up getting a few hundred dollars worth of (used) tools, I am now going on to the national competition in June.
Some more pics:
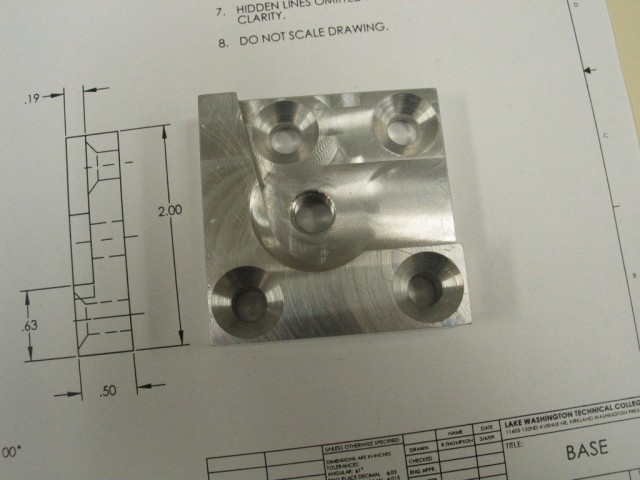
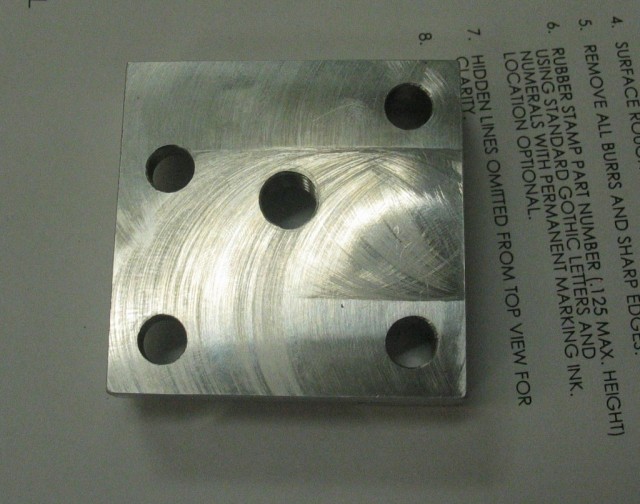
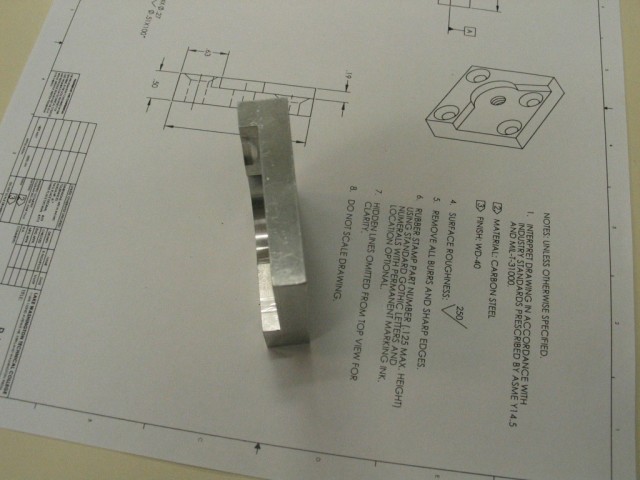
If you want to see my code, you can view it in nice colorful glory here:
Robbie's G-codeFor those who didn't read:
I TOOK FIRST PLACE AT THE STATE LEVEL CNC MILLING COMPETITION AT THE SECONDARY LEVEL!!!!!!Impressed? You -ought- to be.
-RobbieThe1st